Industry partnerships propel Singh’s research to new horizons
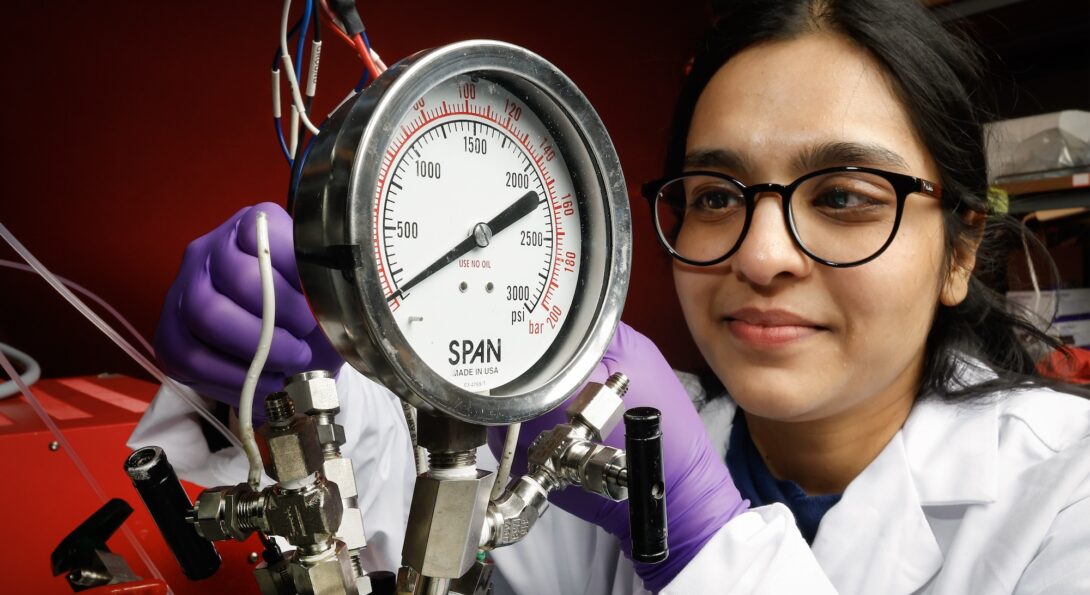
block Heading link
Meenesh Singh, associate professor in the chemical engineering department at UIC, was recently awarded four industrial grants to develop various green technologies. The four grants he received include more than $500,000 in support from Saudi Aramco Technologies Company (SATC), eN-RAMPS LLC, and renewed support from General Ammonia Co, and Braskem America Inc.
Singh is the principal investigator on eight active grants with a total of about $3 million to his lab.
Saudi Aramco
Singh’s project with Saudi Aramco aims to help mitigate carbon emissions and focuses on a fully integrated electrochemical system to capture carbon dioxide (CO2) from the air and convert it to high-commodity liquid chemicals and fuels.
“We utilize CO2 as our carbon source and hydrogen water (H2O), which can be used to make all sorts of organic compounds,” Singh said. “Over 35 billion tons of CO2 was emitted in 2022 by burning fossil fuels. While this is a global concern for climate change, it also presents an opportunity to utilize a freely available source of carbon in the air to support our chemical and fuel supply sustainably.”
This is where the partnership between Singh and SATC comes in. They aim to produce fossil-free green chemicals with a substantially lower carbon footprint by using renewable electricity and CO2 from the air. The goal is to develop scalable CO2 capture and conversion processes to produce green chemicals efficiently.
The conversion of CO2 from the air and water into liquid chemicals such as alcohols, ketones, and organic acids holds immense potential for decarbonizing various industries. Alcohols like methanol and ethanol serve as versatile fuels, powering vehicles, and industries while reducing dependency on fossil fuels. Ketones, including acetone, find applications in manufacturing solvents, resins, and pharmaceuticals, offering eco-friendly alternatives to traditional petroleum-derived chemicals. Organic acids like formic acid and acetic acid play pivotal roles in diverse sectors, from food preservation to pharmaceutical production, contributing to the shift towards sustainable practices.
“This innovative approach not only tackles the escalating levels of CO2 emissions but also presents a sustainable solution for fuel production. By harnessing CO2 as a feedstock, scientists can mitigate greenhouse gas emissions while simultaneously creating valuable products,” Singh said. “This strategy aligns with global efforts to combat climate change and transition towards a greener, more sustainable future.”
The Saudi Aramco project will help the engineers discover the right catalyst for chemical production. From there, Singh and his team can explore different catalysts for different products, which would make their long-term vision of a one-part system possible.
General Ammonia
Ammonia is mostly made up of nitrogen, found in the air and in smaller compounds. As the process of producing ammonia is quite energy intensive, Singh and his team will work to reduce emissions within that process. They plan to take that first process from their previous research grant work, which was built to utilize nitrogen molecules, to make ammonia.
Taking nitrogen from the atmosphere and H2O makes ammonia.
“We can identify and develop a novel high-pressure reactor, which could take pressurized nitrogen and convert it to ammonia at a very high selectivity rate,” Singh said. “Current densities are the rates of ammonia production, so we were able to increase the rate of ammonia production with high selectivity, as in what percentage of the rate goes into ammonia production versus something else.”
Related to nitrogen, ammonia is exclusively the chemical of interest for General Ammonia, but Singh and his team are also interested in combining CO2 and nitrogen. A range of products are only carbon-containing products whereas ammonia is only a nitrogen-containing product, but the carbon and nitrogen together you can make urea, which is a fertilizer.
Ammonia exists at a high-pressure ambient temperature, which is different than CO2, so Singh said the design considerations and scale up strategies are very different between the two projects. He added his team plans to pursue a scale-up strategy as they have received follow-up funding, which will again give us resources to conduct those scale up studies.
Braskem America
As the second grant Singh has been awarded from Braskem, focused on a fully integrated electrochemical system, Singh aims to optimize energy efficiency.
“CO2 also comes from the exhaust of power plants,” Singh said. “The company wants to take that exhaust, capture it, and convert that to ethylene. Ethylene is the starting molecule to make plastics such as polyethylene, the most commonly produced plastic.”
The renewal grant has allowed Singh and his team to conduct a week-long continuous operation of an integrated carbon capture and conversion unit. In turn, this will help them to identify some implications of the long-term operation of a fully integrated electrochemical system for the capture of CO2 from flue gas and converted to ethylene.
During the Braskem project in phase 1, Singh has been developing CO2 capture and conversion unit prototypes and achieved target performances using flue gas.
If ethylene can be made sustainably, it would make a huge impact, and help reduce existing levels of CO2 and nitrates in the environment.
eN-RAMPS
Singh’s startup, eN-RAMPS LLC, is developing a screening system to identify various pharmaceutical compounds to understand the stability of active pharmaceutical ingredients . To speed up that process, Singh and his team are developing a high throughput screening system that will be extended to screen lipid nanoparticles, such as those to make the COVID-19 vaccines.
This will also enable them to redesign the system to create a high throughput screening using microfluidics.
“For the high throughput system, our interest was generally toward the discovery side and the importance of microfluidics,” Singh said. “We learned about the gap in the market that there are currently no microfluidics screening systems, so we started working toward creating that and fitting in some of the applications. Specifically, one application was the pharmaceutical field.”